Creating an asset monitoring center for small and medium manufacturing companies
The term manufacturing company normally brings to mind images of large industrial plants with thousands of workers. However, small family-owned businesses make up the largest proportion of the sector.
According to AMT – The Association for Manufacturing Technology, 97% of the manufacturing firms in the United States have less than 500 employees, and 73% have less than 20 employees. Similar numbers are also seen in Canada, where Plant Magazine reports that 60% of all small and medium manufacturing companies (SMMs), including industrial service providers (i.e., OEMs and maintenance companies) are also family-owned. In fact, SMMs play an important role in economies all over the world.
While the reasons for their success rely directly on the dynamics of being small and family-owned, the same is true for the challenges they face. Michael P. Collins, a manufacturing consultant, explains that one of the main hurdles for SMMs is resource limitation, using the acronym FACTS to summarize it:
“F – Fear of making a wrong decision
A – Limited access to capital
C – Cash flow problems
T – Time constraints
S – Small or no staff”
Collins also says that small manufacturers are just not smaller versions of large manufacturers, therefore, solutions devised and successfully applied to giant manufacturers cannot simply be offered in a smaller size. In India, a survey showed that family businesses were more reluctant in adopting new manufacturing technologies, citing “non-availability of trained personnel, incompatibility with the companies’ existing set-up, and limitations of the existing technology” as reasons for it.
So, in the context of condition monitoring and predictive maintenance, how can these small companies also get the benefits of increased operational equipment efficiency (OEE), as improved uptime and productivity, without losing sight of their particularities?
Easy access to quality hardware
With the FACTS chart in hand, we already know that buying new machinery to become Industry 4.0 compatible is out of the question, either because of limited access to capital or sensibility to wrong decisions. Fortunately, gone are the times when quality hardware was expensive. As technology becomes widespread and vibration sensors reach a lower price point, almost everyone will have access to decent-quality hardware. The other elements of online condition monitoring ecosystem, like data storage and transmission, are also becoming more accessible.
Open ecosystems for flexibility
But the benefits of good hardware to SMMs can be lost if they necessarily come attached to data storage and analytics plans that are either too expensive or oversized to their needs. Software that requires data scientists, or experts in signal processing, or that has excess false alarms is simply not going to be used.
It is now apparent that the preferred solutions are those that enable their vibration specialist (either in-house or a trusted supplier) to answer simple questions: “which machines need to be prioritized?” and “what should be done with them?”. They also have to be compatible with different models of sensors. We have made a commitment to open ecosystems in Industrial IoT, click here to read more about it.
Workflow that doesn’t eliminate industrial specialists
Reliability or maintenance or condition monitoring specialists are an asset for any industrial service company, but SMMs are even more reliant on them. They create long and close relationships with their professionals, in which deep knowledge of the machines and processes are developed. An AI or analytics solution can’t simply propose replacing these specialists. It should instead enable them to optimize their work routine while keeping the diagnostics and the recommendations in their hands.
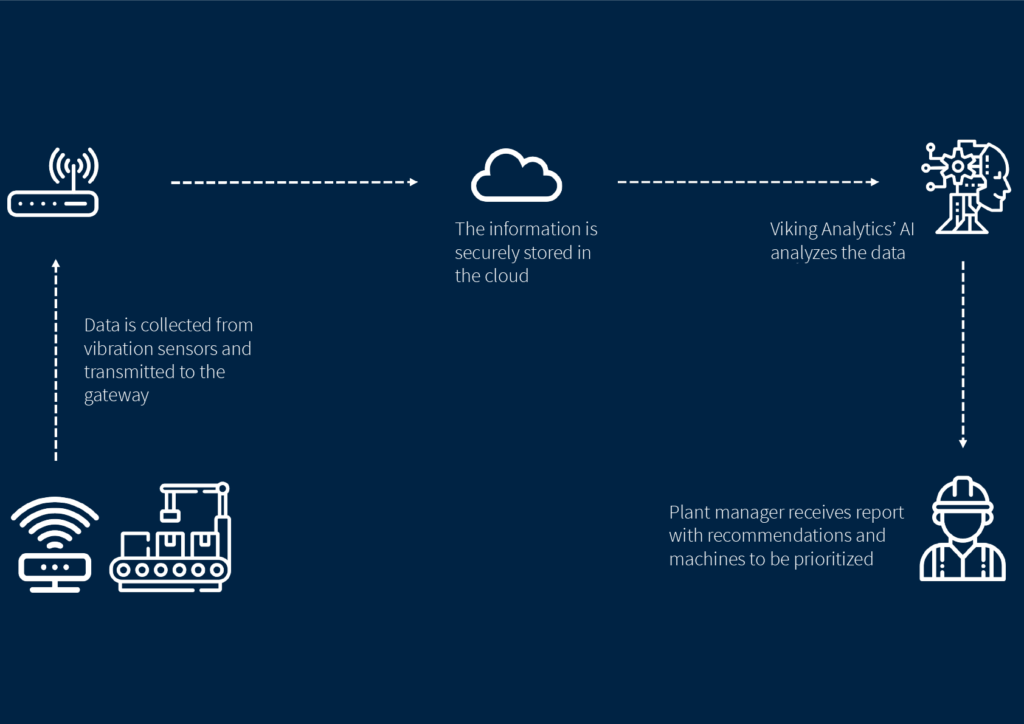
Keep it simple
SMMs’ resources and personnel are mostly dedicated to their core business, and everything else must aim at taking burdens off their backs.
- Simple management, so they don’t need to spend time handling different sensor or cloud or software vendors for each part of the system.
- Simple deployment, that unifies data insights, sensor, storage, and analytics in a single offering.
- Simple purchase, with affordable and flexible plans (like leasing or subscription) so SMMs can avoid worrying about high CAPEX or how the new hardware will look in the balance sheet.
Simplicity lowers the adoption barrier and allows these companies to get started with digitalization and setting up their own predictive maintenance center.
These are the reasons that led us to create a subscription model of MultiViz Vibration, packing together sensors, storage and analytics, for SMMs, including maintenance companies, OEMs and manufacturers. Click here to learn more about it.
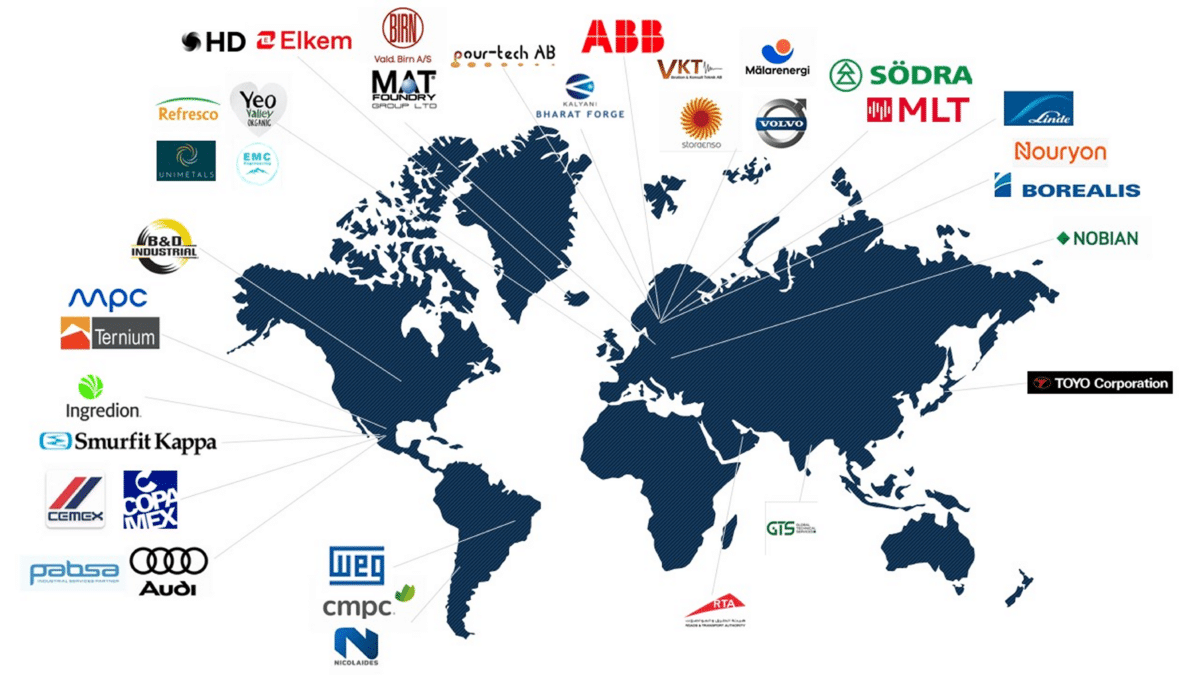